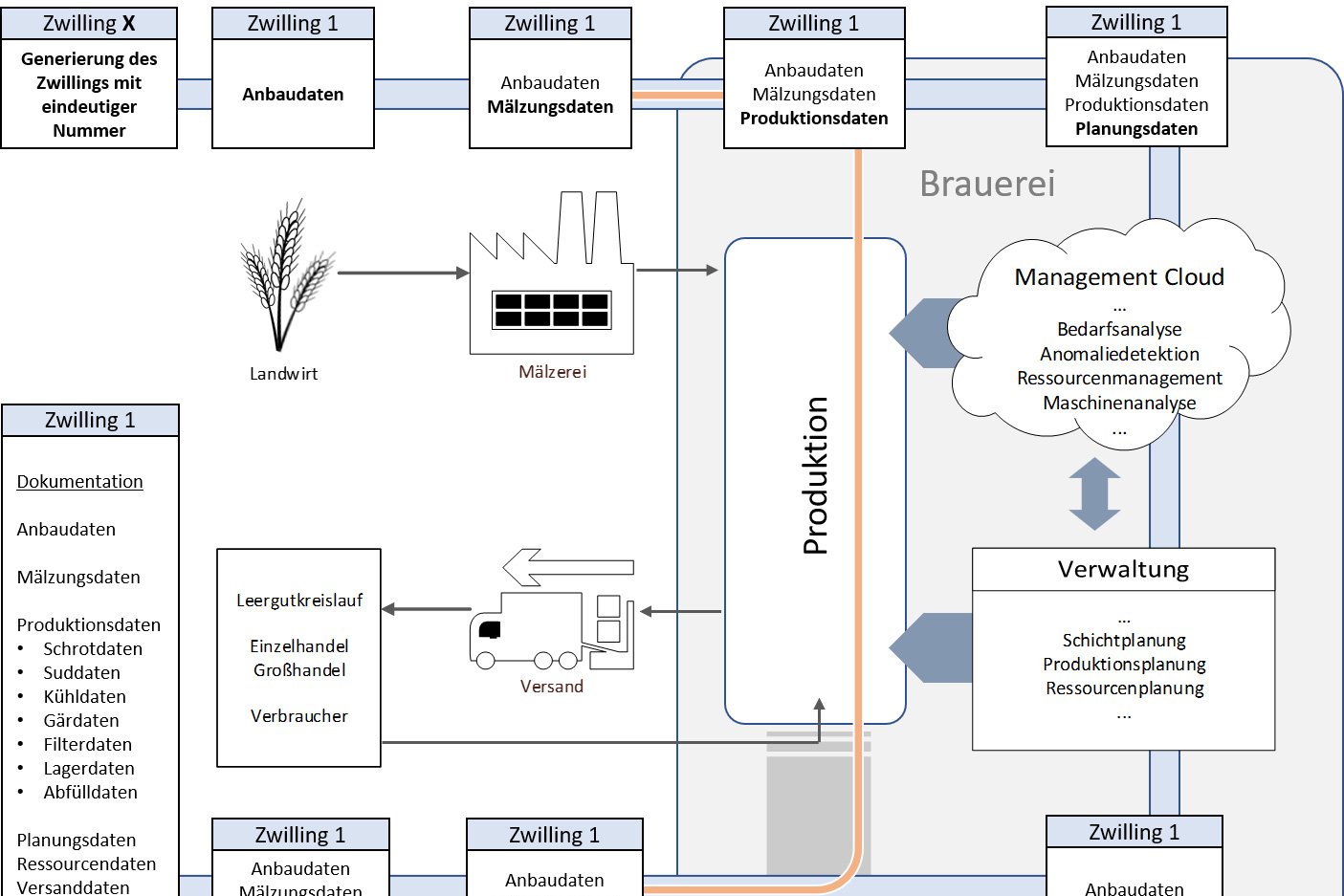
Autor | Institution |
---|---|
Ronny Takacs | Lehrstuhl für Brau- und Getränketechnologie, TUM |
Roman Werner | Lehrstuhl für Brau- und Getränketechnologie, TUM |
Dominik Geier | Lehrstuhl für Brau- und Getränketechnologie, TUM |
Prof. Thomas Becker | Lehrstuhl für Brau- und Getränketechnologie, TUM |
Datum | 14. August 2019 |
Ausgabe | 3 |
Jahrgang | 87 |
Seitenzahl | 121-122 |
Die Zahl der IoT-fähigen (Internet of Things) Geräte wird in den kommenden Jahren auf über 20 Milliarden ansteigen [1]. Die damit einhergehende steigende Informationsdichte und Datengeschwindigkeit bieten der Industrie neue Möglichkeiten zur Produkt- und Prozessüberwachung, zur Erhöhung des Vernetzungsgrades sowie zur Integration von Messstellen, welche bis dato keine echtzeitfähige Prozessanbindung hatten. Daraus ergeben sich Konzepte und Strategien, die in die Entscheidungsfindung und die Qualitätssicherung von Produktionsprozessen einfließen. Insbesondere die sogenannten digitalen Zwillinge haben erfolgreich Einzug in die Industrie gehalten und haben das Potential, die Abläufe entlang der gesamten Wertschöpfungskette zu revolutionieren.
Aufbau digitaler Zwillinge
Digitale Zwillinge sind das virtuelle Abbild eines physischen Objekts oder Prozesses und benötigen Sensoren, über die sie mit der realen Welt verbunden sind. Änderungen am realen Produkt oder Prozess müssen in Echtzeit in das virtuelle Abbild gespiegelt werden, damit beide Varianten stets kongruent sind. Das Konzept der digitalen Zwillinge bietet die Möglichkeit, den aktuellen Zustand eines Produkts entlang des gesamten Produktions- bzw. Lebenszyklus zu ermitteln. Durch die Integration der Anlagenkomponenten in den digitalen Zwilling wird zusätzlich zum Produktstatus auch der Prozess selbst erfasst und die dynamischen Abläufe sowie das Verhalten der einzelnen Systembestandteile während der Prozessierung in Echtzeit digital abgebildet. Aus diesem Grund sieht die Konzeption der digitalen Zwillinge vor, dass diese untereinander und mit höheren Architekturebenen [2], z.B. Management-, Verwaltungs- und Planungsdienste, kommunizieren können. Somit kann nicht nur jedes Produkt mit einer spezifischen Batch-Nummer ein virtuelles Abbild in Form eines digitalen Zwillings in einer IoT-Cloud haben, sondern auch einzelne Maschinen oder ganze Produktionslinien. Ansätze aus dem Bereich des maschinellen Lernens sind dabei eine adäquate Methode, um die großen Datenmengen zu strukturieren und auszuwerten. Es ist jedoch zu beachten, dass die Fülle an Daten oft eine strikte Festlegung definierter Systemgrenzen voraussetzt.
Beim Einsatz von digitalen Zwillingen und der dazugehörigen Peripherie werden in der Wertschöpfungskette alle relevanten Informationen vom Feld bis zum Verbraucher digitalisiert [3], siehe Abbildung 1.
Rückverfolgbarkeit „vom Korn bis in die Flasche“
Nachfolgend wird ein Anwendungsbeispiel aus dem Qualitätsmanagement von Bier dargestellt, wobei die Rückverfolgbarkeit chargenspezifisch vom Korn bis in die Flasche umgesetzt wird. Die Besonderheit der digitalen Zwillinge liegt darin, dass die Informationen des digitalen Zwillings über die Prozesskette bis hin zum Verbraucher durch weitere digitale Zwillinge aus dem B2B-Bereich (Gerstenanbaudaten, Mälzungsdaten, Hopfenspezifikationen, Speditionsdaten etc.) oder der eigenen Produktion (Suddaten, Hefemanagement, Brauwasserdaten etc.) ergänzt werden.
Abbildung 2 zeigt schematisch den Verlauf und das Informationswachstum eines digitalen Zwillings (blauer Verlauf). Dieser digitale Zwilling wird zu Beginn des Produktlebenszyklus generiert und im Verlauf der Zeit mit neuen Informationen aus den Prozessen und weiteren interagierenden digitalen Zwillingen ergänzt. Diese Daten stammen u.a. von Zwillingen der eigenen Produktion sowie aus der Datenfreigabe im B2B-Bereich, die durch digitalen Datentransfer von den jeweiligen Unternehmen gesendet werden. Die in der Brauerei erfassten Daten (Abb. 2, orangefarbener Verlauf) können Produktionsparameter (z.B. Maischzeiten bzw. -temperaturen), Anlagenparameter (z.B. Ausstattung des Maischbottichs) und Labordaten (z.B. Viskosität) enthalten. Zusätzlich zu diesen Produktionsdaten werden auch Stördaten und Human-Machine-Interface-(HMI)-Eingaben abgebildet.
In jedem Produktionsschritt werden so dem übergeordneten digitalen Zwilling weitere Informationen über das Produkt und dessen Herstellung hinzugefügt. Durch die Verknüpfung dieser Informationen wird eine lückenlose Betrachtung des Produktlebenszyklus ermöglicht. So kann z.B. bei Auftreten einer abweichenden Bierqualität die Betrachtung auf Umgebungs- bzw. Produktionsparameter sowie Rohstoffdaten chargenweise ausgeweitet werden.
Weitere Anwendungen
Ebenso können die Daten aus Management-, Verwaltungs- und Planungsdiensten, beispielsweise Personal- und Ressourcenplanung, mit den Daten der digitalen Zwillinge synchronisiert oder nachfolgenden Analysezwecken zugänglich gemacht werden [3, 4]. Dabei können durch Methoden der künstlichen Intelligenz oder des maschinellen Lernens neue Querverbindungen und Muster erkannt werden. Durch die Vernetzung mit diesen höheren Architekturebenen und der sich neu ergebenden Auswertungsmöglichkeiten, können Abschätzungen von der zu erlangenden Produktqualität oder Maschinenlebensdauer in Echtzeit erstellt werden.
Ein besonders hervorzuhebender Vorteil ist dabei die prädiktive Analyse zukünftiger Ereignisse (Predictive Analytics). So können z.B. Anomalien an Geräten oder Maschinen noch vor Auftreten des eigentlichen Defekts erkannt und gegengesteuert werden. Damit ist es möglich, Reparaturen im Vorfeld geplant durchzuführen und somit Ausfallzeiten und Fehlproduktionen zu minimieren. Diese Systeme sind durch ihre Datendichte und ihren Aufbau in der Lage, eigenes Expertenwissen zu generieren und somit Anomalien eigenständig zu erkennen. Dieser hohe Vernetzungsgrad über die eigenen Produktionsgrenzen hinweg ermöglicht eine Bewertung über die gesamte Wertschöpfungskette.
Die Integration von digitalen Zwillingen erfordert jedoch immer eine detaillierte Analyse des bestehenden Produktionsprozesses mit Produktionsplänen, SCADA-Plänen (Supervisory Control and Data Acquisition) und anderen Informationen des ERP-Systems (Enterprise Resource Planning). So kann es bei bestehenden Anlagen erforderlich werden, neue Messstellen in den Prozess einzubinden. Die Tiefe der Datenerhebung ist jedoch nicht limitiert. Es sollten stets grundlegende Daten, wie z.B. Temperaturen, Zeiten, Leitwerte oder Füllstände, integriert werden. Detailliertere Abbildungen sind jedoch immer – mit entsprechendem Einsatz – möglich. Letztlich muss bei bestehenden Produktionsprozessen ein sogenanntes Big Picture erstellt werden, welches nicht nur den physikalischen Produktionsverlauf, sondern auch andere Datenströme, Produktionsverantwortlichkeiten und Stakeholder berücksichtigt. Soll das System B2B ausgebaut werden, muss zudem eine Standardisierung sowie normierte Vorverarbeitung der Daten erfolgen.
Der Einsatz von digitalen Zwillingen und die damit einhergehende Digitalisierung von physischen Objekten und/oder Prozessen wird sich zu einem wesentlichen Bestandteil der Produktion entwickeln und es bestehen derzeit zahlreiche Ansätze der digitalen Auswertung, Analyse, Optimierung und Modellierung [6]. Die intelligente Verknüpfung von digitalen Zwillingen mit Managementsystemen zeigt dabei neue Möglichkeiten der Produktion, der Überwachung und der Prozesssteuerung auf. Bei entsprechender Granularität bieten digitale Zwillinge zahlreiche Möglichkeiten zur virtuellen Inbetriebnahme, zum Produktlebenszyklusmanagement, zur Schulung von Maschinenführern, Predictive Analytics, Rückverfolgbarkeit und Erkennung von Funktionsstörungen und sie eröffnen zudem neue Geschäftsmöglichkeiten.
Danksagung
Das Projekt und die Activity 18110 Digital Twin Management wurde von der Europäischen Union über das Europäische Institut für Innovation und Technologie und der Wissen- und Innovationsgemeinschaft EIT Food gefördert.
Literatur
1. Deloitte. 2017. Grenzenlos vernetzt. Smarte Digitalisierung durch IoT, Digitale Zwillinge und die Supra-Plattform; www2.deloitte.com; accessed 17 Juli 2019.
2. Kreutzer, R. T.; Sirrenberg, M.: Künstliche Intelligenz verstehen. Grundlagen – Use-Cases – unternehmenseigene KI-Journey; Springer Fachmedien Wiesbaden; Springer, Gabler, Wiesbaden, 2019.
3. Fend, L.; Hofmann, J., (Eds.): Digitalisierung in Industrie-, Handels- und Dienstleistungsunternehmen. Konzepte – Lösungen – Beispiele; Springer, Gabler, Wiesbaden, 2018.
4. Borgmeier, A.; Grohmann, A.; Gross, S. F.: Smart services und Internet der Dinge. Geschäftsmodelle, Umsetzung und Best Practices: Industrie 4.0, Internet of Things (ioT), Machine-to-Machine, Big Data, Augmented Reality Technologie; Hanser, München, 2017.
5. Hehenberger, P.; Bradley, D. (Eds.): Mechatronic futures. Challenges and solutions for mechatronic systems and their designers. Springer, Schweiz, 2016.
6. Boschert, S.; Rosen, R.: „Digital Twin – The Simulation Aspect“; in Mechatronic futures. Challenges and solutions for mechatronic systems and their designers, P. Hehenberger and D. Bradley (Eds.),
Springer, Schweiz, 2016, S. 59– 74. DOI=10.1007/978-3-319-32156-
1_5.
Name | Datei |
---|---|
Die Zukunft der Produktion - Industrie 4.0 mit digitalen Zwillingen und vernetztem Management |
![]() |