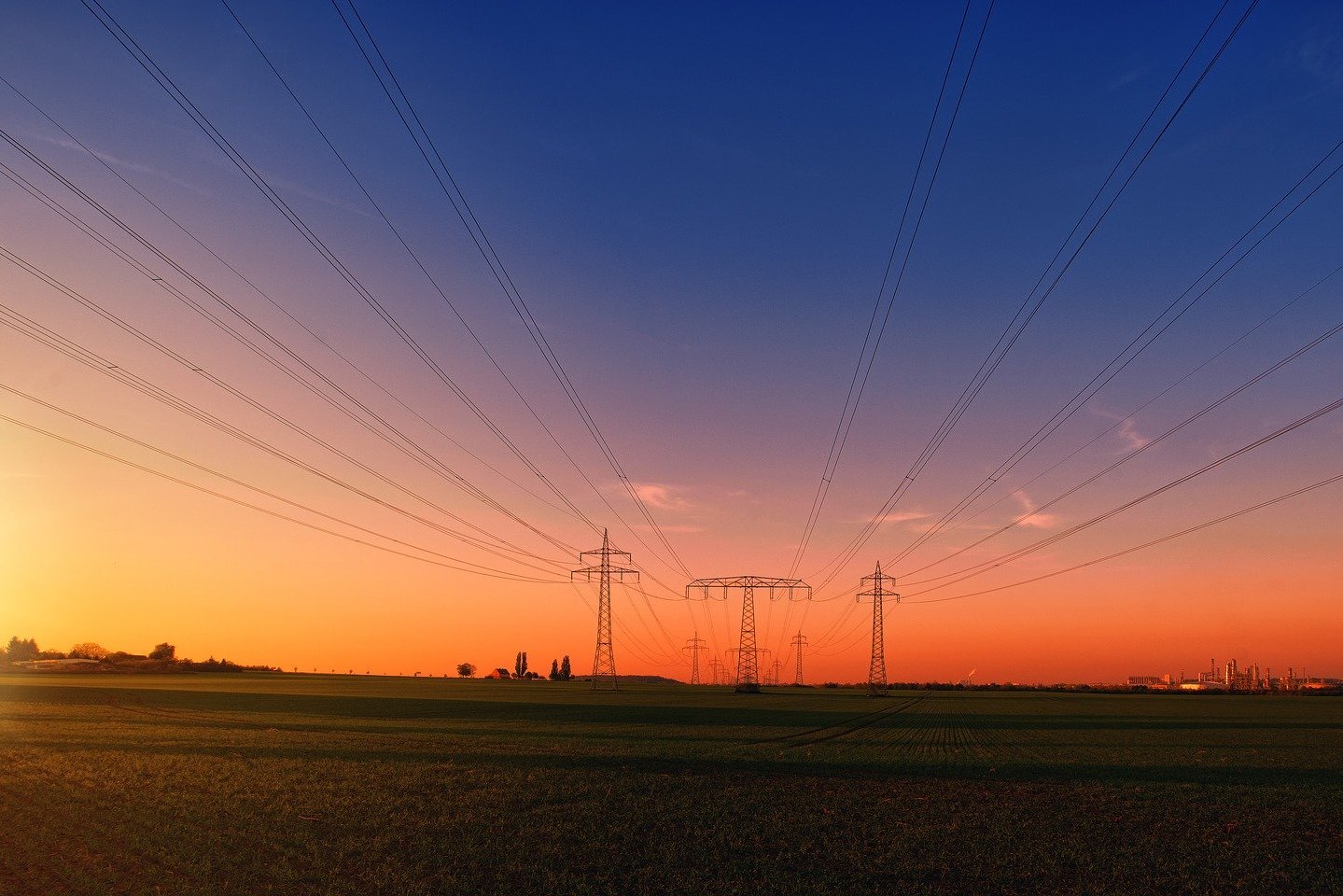
Autor | Institution |
---|---|
Sebastian Schmid | Lehrstuhl für Lebensmittelchemie und molekulare Sensorik, Arbeitsgruppe Wassertechnologie, TUM |
Prof. Thomas Hofmann | Lehrstuhl für Lebensmittelchemie und molekulare Sensorik, TUM |
Dr. Karl Glas | Lehrstuhl für Lebensmittelchemie und molekulare Sensorik, Arbeitsgruppe Wassertechnologie, TUM |
Datum | 30. Oktober 2019 |
Ausgabe | 4 |
Jahrgang | 87 |
Seitenzahl | 148-153 |
Energie- und Klimapolitik
Vor Kurzem übergab der Sachverständigenrat zur Begutachtung der gesamtwirtschaftlichen Entwicklung der Bundesregierung ein Sondergutachten zu möglichen Reformoptionen in der Klimapolitik. Der ersten der insgesamt sechs Kernbotschaften ist zu entnehmen, dass es der volkswirtschaftlich kosteneffizienteste Weg sei, einen sektorübergreifend einheitlichen Preis für Treibhausgasemissionen zu etablieren, wodurch die Einzelentscheidungen der Haushalte und Unternehmen effizient koordiniert werden können [1]. Ebenso sind Innovationen entscheidend, um die Klimaziele zu erreichen [1].
Im Sondergutachten wird darauf hingewiesen, dass eine Ausweitung der CO2-Bepreisung zusätzliche Belastungen für Unternehmen und Haushalte zur Folge hat [2]. „Die Belastungen für Unternehmen unterscheiden sich deutlich über Branchen hinweg und hängen von der Energieintensität und den Überwälzungsmöglichkeiten auf Verbraucher ab“ (S. 87) [2]. Eine Abschätzung der Belastung von Unternehmen wurde anhand zweier Szenarien durchgeführt (vgl. hierzu Abb. 1). Hierbei wird angenommen, dass „[...] entlang der Wertschöpfungskette alle Kostenerhöhungen auf nachfolgende Wirtschaftszweige überwälzt werden können. Die tatsächliche Belastung wird für einen Wirtschaftszweig umso höher ausfallen, je geringer das Ausmaß der Überwälzung auf nachfolgende Wirtschaftszweige ist“ (S. 90) [2].
Im Jahresbericht 2018/19 der Bundesvereinigung der Deutschen Ernährungsindustrie e.V. wird herausgestellt, dass die Verhandlungspositionen zwischen Lebensmittelherstellern und Lebensmitteleinzelhandel aufgrund einer starken Konzentration auf Seiten der Handelsunternehmen ungleich verteilt sind [3]. Diese Situation bedingt einen harten Qualitäts- und Preiswettbewerb unter den Lebensmittelherstellern, sodass die Mehrheit der Hersteller eine Steigerung von Produktionskosten nicht an den Handel weitergeben kann [3]. Mit Blick auf die Brauwirtschaft ist anzumerken, dass die Verkaufspreise im Handel die tatsächlichen Herstellungskosten oftmals nur unzureichend widerspiegeln [4]. Im europäischen Vergleich ist die Lebensmittelindustrie in Deutschland zudem mit überdurchschnittlich hohen Preisen für Strom (0,150 EUR/kWh ohne MwSt) und Erdgas (0,026 EUR/kWh ohne MwSt) konfrontiert [3].
Unbeschadet kontrovers geführter Diskussionen suggeriert die Berichterstattung in den Medien, dass ein länderübergreifender gesellschaftlicher Konsens aus Politik und Bevölkerung besteht, der die Einführung einer CO2-Bepreisung zur Erreichung der europäischen Klimaziele [5] trägt. Insbesondere die Brau-, Milch- und Zuckerwirtschaft zählen zu den energieintensiven Branchen der Lebensmittelindustrie [6–11]; unabhängig von der Ausgestaltung einer CO2-Bepreisung ist zu vermuten, dass hierdurch die Kosten für die Energieversorgung einer Brauerei ansteigen könnten.
Energieverwendung in der Brauerei
Der Anteil an Wärme bzw. elektrischer Energie am Gesamtenergiebedarf einer Brauerei liegt bei ca. 75 bzw. ca. 25 Prozent [12]. Einen Eindruck über den Energieverbrauch bei der Bereitung und Abfüllung von Bier geben die Tabellen 1 und 2. Die überwiegende Zahl der Brauereien ist bei der Versorgung mit Wärme auf fossile Brennstoffe und bei der Bereitstellung elektrischer Energie auf die Elektrizitätswirtschaft angewiesen [13, 14]; siehe dazu auch Tabelle 3. Eine Studie im Auftrag der Vereinigung The Brewers of Europe zeigt, dass der Anteil erneuerbarer Energien am Gesamtenergieverbrauch der europäischen Brauwirtschaft in den Jahren 2008, 2009 und 2010 lediglich bei 5,0 Prozent, 4,8 Prozent und 5,3 Prozent liegt [15]. Aktuelle Zahlen aus Deutschland für den Wirtschaftszweig Getränkeherstellung legen nahe, dass erneuerbare Energien bisher nur in geringem Umfang genutzt werden [16]. In Zusammenhang mit der Schwankungsbreite von Verbrauchswerten sei abschließend erwähnt, dass der spezifische Energieverbrauch einer Braustätte auf eine Vielzahl an Einflussgrößen, wie z.B. den Ausstoß, die technische Ausstattung, das Produktionsprogramm oder die geographische Lage zurückzuführen ist [14, 17]; den Einfluss der Betriebsgröße verdeutlicht Tabelle 4.
Zur Zeit der Dampfbiere
Mit Verbreitung der Dampfbierbrauerei um das Jahr 1800 ist in der Brauwirtschaft bereits ein umfängliches Bewusstsein hinsichtlich einer rationellen Energieverwendung vorhanden; einen Eindruck hiervon mögen ausgewählte Arbeiten vermitteln.
Poppe berichtet im Jahr 1834 über einen Braukessel, dessen sich die englischen Brauer bedienen (siehe Abb. 2) [23]. Der obere Teil dieses Kessels ist mit einer Pfanne ausgestattet, die der Erwärmung von Wasser und Würze dient [23]. Hierfür werden die heißen Dämpfe, die über der Flüssigkeit im Kessel aufsteigen, mittels Dampfröhren, die bis nahe auf den Boden der Pfanne reichen, in die darin befindliche Flüssigkeit eingeleitet, wodurch die Flüssigkeit in der Pfanne ohne zusätzliches Brennmaterial erwärmt werden kann [23]. Zum Maischen im Holzbottich vermerkt Poppe, dass auch dies durch ein direktes Einleiten von Wasserdampf zu bewerkstelligen ist; ebenso ist es möglich, Wasser in hölzernen Gefäßen in sehr kurzer Zeit und mit sehr wenig Brennmaterial zum Sieden zu bringen [23].
Mit dem Hinweis, dass „durch die Benützung eines Meischbottichs [sic!] und durch die Nicht-Benützung der, aus den kochenden Meischen [sic!] entweichenden Dämpfen“ (S. 4) [24] Wärme beim Brauen verloren geht, eröffnet Müller im Jahr 1854 eine Diskussion der Vorzüge seines Brauverfahrens, die von umfangreichen Berechnungen zu Wärmeaufwand und -einsparung gestützt wird. Daneben wird der Einfluss von Sudrhythmus und -größe auf den Bedarf an Arbeitskräften sowie an Brennmaterial erörtert. Wird beispielsweise nur ein Sud am Tag gesotten, führt dies zu einer Auskühlung der Pfannenmauern während der Sudpausen und zu einem Mehraufwand an Brennmaterial beim darauffolgenden Sud, da die Mauern erst wieder in den „frühern [sic!] Hitzegrad“ (S. 24) [24] zu versetzen sind. Dieser Wärmeverlust wäre vermeidbar, falls ein Sud „unmittelbar nach dem vorgegangenen unternommen werden könnte“ (S. 24) [24]. An einem Lehrbeispiel zeigt Müller, dass die Aufteilung eines „großen“ Sudes auf mehrere „kleine“ Sude den Mehraufwand an Personal aufgrund einer Einsparung an Brennmaterial kompensieren kann [24].
Im Jahr 1858 nimmt Ebert die jährlich steigenden Holzpreise zum Anlass, um über den Bedarf an Tannen- und Fichtenholz in Abhängigkeit des zur Anwendung kommenden Brauverfahrens, wie z.B. der „alten empirischen Methode“, „bei rationeller Heizvorrichtung“ oder der „Brauerei mittels Dampf“ zu berichten [25]. Ergänzt werden diese Ausführungen um einen Vergleich der „Hitzkraft“ weiterer Holzarten, wie z.B. Ahorn, Birke oder Eiche mit der von Tannen- und Fichtenholz [25]. Als alternative Brennstoffe sind nach Ebert Torfziegel sowie Braun- und Steinkohlen geeignet [25]. Ein Vergleich der „Hitzkraft“ verschiedener Kohlearten und -qualitäten mit der von Fichtenholz zeigt, dass durch die Verwendung von Kohlen mitunter erhebliche Einsparungen an Brennmaterial zu erreichen sind [25]. Ob die Materialeinsparungen die Mehrkosten bei der Beschaffung der Kohlen aufwiegen, bleibt allerdings unklar.
Mit seinem um das Jahr 1859 patentierten Dampfbrau- und Kühlapparat verfolgt Habich eine „[…] Theilung [sic!] der Arbeit desselben, so daß [sic!] die einzelnen Brauoperationen – Einmaischen, Abläutern, Erhitzen des Nachgußwassers [sic!], Hopfenkochen und Eindampfen der Würze – in verschiedenen Gefäßen gleichzeitig nebeneinander ins Werk gesetzt werden“ (S. 3) [26]. Die einzelnen Gefäße des Apparates werden „[…] zur großen Bequemlichkeit des Brauers terassenförmig [sic!]“ (S. 12) [26] aufgestellt, sodass die Flüssigkeit ohne Zuführung mechanischer Energie von einem in das andere Gefäß abfließen kann. Um die Oberfläche für den Wärmeaustausch zu vergrößern, wird der Kesselboden in Rinnen bzw. Falten gebogen [26]. Ein Schwerpunkt liegt zudem auf der Rückgewinnung von Wärme beim Kochen und Kühlen der Würze. Bemerkenswert ist hierbei der mehrstufige sowie auf zwei Bottiche aufgeteilte Würzekühler, bei dem sowohl Brunnenwasser als auch Eiswasser zum Kühlen der Würze verwendet werden, um möglichst heißes Brau- und Betriebswasser zu gewinnen [26]. Für den Betrieb seines Apparats gibt Habich dem Brauer ein detailliertes Produktionsablaufschema an die Hand; so können bis zu acht Sude pro Tag gesotten werden [26].
Erwähnenswert ist, dass die Arbeiten von Poppe [23], Müller [24], Ebert [25] und Habich [26] sowohl Überschneidungen mit dem Stand der Technik (vgl. Schu und Ruß [27]) als auch mit verhältnismäßig aktuellen Entwicklungen (vgl. Gattermeyer [28] oder Holmes et al. [29]) aufweisen.
Die „Ölkrisen“
Einen Überblick über den Energieverbrauch der Brau-, Milch- und Zuckerwirtschaft in den Jahren 1978 bis 1985 gibt Abbildung 3. Mit Blick auf die Ölpreisschocks in den Jahren 1973/74 sowie 1979/80 referiert Pensel auf dem EBC-Kongress 1981, dass eine Gefährdung der Versorgungssicherheit energetische Einsparmaßnahmen erforderlich macht; ebenso sei die Umweltbelastung zu bedenken, die mit einer Nutzung fossiler Energieträger einhergeht [13]. Dennoch beschreibt Pensel alternative Energiequellen, wie z.B. Wind- und Sonnenenergie als „Wohlstandsenergie“ (S. 631) [13], deren Anwendungsmöglichkeiten in der Brauerei begrenzt seien. Zweckmäßige Maßnahmen zur Steigerung der Energieeffizienz sind z.B. Apparate und Anlagen bzw. Verfahren zur Energierückgewinnung beim Kochen und Kühlen der Würze oder zur „Verbesserung des energetischen Nutzeffektes“ (S. 635) [13]. Hierbei ist allerdings zu bedenken, dass oftmals betriebswirtschaftliche Gründe einer Umsetzung von Effizienzmaßnahmen entgegenstehen; steigende „Energiekosten“ können Investitionsentscheidungen jedoch positiv beeinflussen [13].
Weiterhin empfiehlt Pensel eine energiewirtschaftliche Betriebskontrolle, da die Brauwirtschaft noch einige Zeit auf fossile Energieträger angewiesen sein wird [13]. In Zusammenarbeit mit dem Bayerischen Brauerbund e.V. gibt er im Jahr 1983 schließlich ein Handbuch für die praktische Betriebskontrolle heraus; nach seiner Erfahrung erfährt die Energiewirtschaft in der Brauerei häufig nur geringe Beachtung [30]. Einer der ersten „Energieleitfäden“ für Brauereien wird im Jahr 1985 vom Landesgewerbeamt Baden-Württemberg veröffentlicht [31]. In Zusammenhang mit den „Ölkrisen“ sei noch das Seminar Energiemanagement in der Brauereiwirtschaft erwähnt, das im Jahr 1989 in Weihenstephan abgehalten wurde. In seiner Eröffnungsansprache betont Meyer-Pittroff, dass „rationeller Energieeinsatz und damit verbundene Umwelt- und Ressourcenschonung keine nationale Aufgabe mehr ist, sondern eine internationale und weltweite“ (S. 2) [32]. Hier wird auch über das Energiebus-Programm der Gemeinschaften berichtet; neben der Durchführung von Energieaudits werden die Energieverbräuche der teilnehmenden Brauereien ermittelt und miteinander verglichen [33].
Zukünftige Herausforderungen
Die „Ölkrisen“ haben der Brauwirtschaft durch eine sprunghafte Verteuerung von Erdöl und -gas die Notwendigkeit einer rationellen Energienutzung bewusstgemacht. Maßnahmen zur Energieeinsparung, wie z.B. die Rückgewinnung und Speicherung von Abwärme, haben hierdurch nahezu ubiquitäre Verbreitung erfahren; diese Entwicklung belegen zahlreiche „Energieleitfäden“ für Brauereien, die eine Umsetzung von Effizienzmaßnahmen sowie eine Verbreitung nachhaltiger Versorgungskonzepte unterstützen sollen [20, 21, 34–37].
Ein weiterer Beleg für das gestiegene Energiebewusstsein der Branche ist das zunehmende Energiebenchmarking; im deutschsprachigen Raum ist der Betriebevergleich Energie für Brauereien seit über 20 Jahren etabliert [38–40]. Mit Blick auf kleine und mittlere Brauereien ist anzumerken, dass oftmals Mittel zur Finanzierung von Effizienzmaßnahmen fehlen, die gewachsene Betriebsstruktur einer Umsetzung entgegensteht oder Vorbehalte gegenüber Änderungen an Apparaten bzw. Verfahren bestehen (Bierqualität) [17, 41]. Dahingegen wird die deutsche Brauwirtschaft, die von kleinen und mittleren Betrieben geprägt ist, als überaus energiebewusst beschrieben; nach Putz et al. wäre eine weitere Verbesserung der energetischen Situation nur durch kapitalintensive Technologiesubstitutionen zu erreichen [42].
Die Abhängigkeit der Brauwirtschaft von fossilen Energieträgern, insbesondere bei der Bereitstellung von Wärme, ist als nicht unerhebliches Zukunftsrisiko zu betrachten. Einerseits sind umfangreiche Reserven an Erdöl und -gas vorhanden, andererseits spiegelt die Erschließung neuer Förderstätten, die hohe Investitionen erfordern, die Nachfragesteigerungen nicht wider. Aktuelle Zukunftsszenarien legen nahe, dass es hierdurch mittelfristig zu Versorgungsengpässen kommen könnte [43, 44].
Unklar bleibt, inwiefern die nachteiligen Rahmenbedingungen im Bereich „Energie“ die Zukunft der deutschen Brauwirtschaft beeinflussen werden. Die europäischen Anstrengungen hin zu einer klimaneutralen Gesellschaft führen in Deutschland zu einer Verteuerung von „Energie“ durch staatlich veranlasste Preisbestandteile, wie z.B. Umlagen und Abgaben. Nachhaltige Energieversorgungskonzepte für die Brauwirtschaft scheinen derzeit nur im begrenzten Umfang geeignet zu sein, um für Entspannung zu sorgen, da eine Umsetzung mit erheblichem technischen und finanziellen Aufwand verbunden ist, wie die Ausführungen von Remus et al. [45], Pöschko und Grasmück [46] oder Schmitt et al. [47] belegen.
Für die europäische Brauwirtschaft ist festzustellen, dass Erdgas bisher nur in geringem Maß durch Biogas substituiert wird [15]. Im großen Umfang wären energetische Einsparungen beispielweise durch die Verwendung von Rohfrucht und Surrogaten oder technischen Enzymen zu erreichen; zudem könnte auf das Kochen der Würze verzichtet werden. An dieser Stelle sei die Arbeit von Russell et al. erwähnt, die unkonventionell Methoden der Bierbereitung behandelt [48].
In Zusammenhang mit der deutschen Energiewende wird abschließend auf die Ausführungen von Fischer zu elektrisch beheizten Braupfannen verwiesen: „Der Gedanke, die Sudhausgefäße statt mit Feuergasen oder mit Dampf unmittelbar mit elektrischem Strom zu beheizen, […] ist wegen der Vorteile naheliegend, an die man zunächst dabei denken wird: Wegfall der Feuerung mit ihrer schlechten Regelbarkeit, hoher Wirkungsgrad, sauberer, völlig staubfreier Betrieb, einfachste Bedienung. Der einzige Nachteil dürfte in der Unwirtschaftlichkeit liegen, wenn der Strom aus Kohle auf dem Weg über eine Dampfkraftmaschine erzeugt wird“ (S. 62) [49].
Literatur
1. Sachverständigenrat zur Begutachtung der gesamtwirtschaftlichen Entwicklung: Aufbruch zu einer neuen Klimapolitik – Kernbotschaften, 2019, https://www.sachverstaendigenrat-wirtschaft.de/fileadmin/dateiablage/gutachten/sg2019/SVR_SG_Kernbotschaften.pdf; Zugriff am: 26.7.2019.
2. Feld, L. P.; Schmidt, C. M.; Schnabel, I. et al.: Aufbruch zu einer neuen Klimapolitik, 2019, https://www.sachverstaendigenrat-wirtschaft.de/fileadmin/dateiablage/gutachten/sg2019/sg_2019.pdf; Zugriff am: 26.7.2019.
3. Bundesvereinigung der Deutschen Ernährungsindustrie: Jahresbericht 2018/2019, 2019, https://www.bve-online.de/download/bve-jahresbericht-ernaehrungsindustrie-2019; Zugriff am: 26.7.2019.
4. Stracke, S.; Homann, B.: Branchenanalyse Getränkeindustrie, 2017, https://www.ngg.net/fileadmin/Fotos_und_Bilder/Branchen/2018-2014/Getraenke/2017_hbs_branchenanalyse_getraenkeindustrie.pdf; Zugriff am: 26.7.2019.
5. Umweltbundesamt: Europäische Energie- und Klimaziele, 2019, https://www.umweltbundesamt.de/daten/klima/europaeische-energie-klimaziele; Zugriff am: 26.7.2019.
6. Nassauer, J.: Energieeinsparung in der Lebensmittelindustrie; in: Heiss, R. (Hrsg.): Lebensmitteltechnologie, Springer-Verlag, Berlin, 2004, S. 509–522.
7. Fleiter, T.; Schlomann, B.; Eichhammer, W.: Energieverbrauch und CO2-Emissionen industrieller Prozesstechnologien – Einsparpotenziale, Hemmnisse und Instrumente, 2013, https://www.isi.fraunhofer.de/content/dam/isi/dokumente/ccx/2013/Umweltforschungsplan_FKZ-370946130.pdf; Zugriff am: 26.7.2019.
8. Energieagentur NRW: Energieeffizienz in Brauereien [ohne Jahr], https://www.energieagentur.nrw/energieeffizienz/energieeffizienz-nach-branchen/energieeffizienz_in_brauerei; Zugriff am: 26.7.2019.
9. Schu, G.: Energy; in: Eßlinger, H.M. (Hrsg.): Handbook of Brewing, Wiley-VCH, Weinheim, 2009, S. 643–664.
10. Austmeyer, K.E.; Röver, H.: Energiebedarf für die Bereitstellung von Lebensmitteln – vom Rohstoff bis zum Verbraucher; in: VDI-Gesellschaft Energietechnik (Hrsg.): Rationelle Energietechnik in der Lebensmittelindustrie. VDI-Verlag, Düsseldorf, 1988, S. 13–34.
11. Blesl, M.; Kessler, A.: Energieeffizienz in der Industrie. Springer Vieweg, Berlin, 2013.
12. Sattler, P.: Energiekennzahlen und -sparpotenziale in Brauereien, 2000, http://www.win.steiermark.at/cms/dokumente/11263981_52485923/5311a767/Energiekennzahlen%20und%20Sparpotenziale%20in%20Brauereien.pdf; Zugriff am: 26.7.2019.
13. Pensel, S.: Notwendigkeit der Energieerhaltung. In: European Brewery Convention (Hrsg.): Proceedings of the 18th Congress. IRL Press Limited, 1981, S. 631–636.
14. Hackensellner, T.; Bühler, T.M.: Effizienter Energieeinsatz im Sudhaus [ohne Verlag] [ohne Ort], 2008.
15. Donoghue, C.; Jackson, G.; Koop, J.H. et al.: The Environmental Performance of the European Brewing Sector, 2012, https://brewersofeurope.org/uploads/mycms-files/documents/archives/publications/2012/envi_report_2012_web.pdf; Zugriff am: 26.7.2019.
16. Statistisches Bundesamt: Statistisches Jahrbuch 2018, 2018, https://www.destatis.de/DE/Themen/Querschnitt/Jahrbuch/statistisches-jahrbuch-2018dl.pdf?__blob=publicationFile; Zugriff am: 8.9.2019.
17. Sturm, B.; Hugenschmidt, S.; Joyce, S. et al.: Opportunities and barriers for efficient energy use in a medium-sized brewery; in: Applied Thermal Engineering 53 (2013), S. 397–404.
18. Hahn, P.; Gertler, M.: Die deutsche Brauwirtschaft in Zahlen 2008, 2009, https://www.brauer-bund.de/download/Archiv/PDF/statistiken/Die%20deutsche%20Brauwirtschaft%20in%20
Zahlen%202008.pdf; Zugriff am: 26.7.2019.
19. Erhorn, T.: Integrierte Energieversorgung in Brauereien. Berlin, Technische Universität Berlin, 1982.
20. The Brewers of Europe: Guidance Note for establishing BAT in the brewing industry, 2002, http://www.brewersofeurope.org/docs/publications/guidance.pdf; Zugriff am: 11.4.2016.
21. European Commission: Reference Document on Best Available Techniques in the Food, Drink and Milk Industries, 2006, https://eippcb.jrc.ec.europa.eu/reference/BREF/fdm_bref_0806.pdf;
Zugriff am: 26.7.2019.
22. Schu, F.; Stolz, F.; Jordan, U. et al.: „Betriebevergleich Energie 1998“; in: Brauwelt 141 (2001), S. 116–120.
23. Poppe, J.H.M.: Die Bierbrauerei auf der höchsten Stufe der jetzigen Vervollkommnung oder die Kunst, die vorzüglichsten deutschen und englischen Biere nach den besten Grundsätzen und den neuesten geprüften Erfahrungen zu brauen. C. F. Osiander, Tübingen, 1834.
24. Müller, A.E.: Das neue Brau-Verfahren mit dem hierzu construirten Apparate; C. F. Wiegand, Pressburg, 1854.
25. Ebert, K.J.: Die Bierbrauerei vom Standpunkte ihrer heutigen Vervollkommnung zunächst für Landwirthe und Brauer; Verlag von Karl André, Prag, 1858.
26. Habich, G.E.: Kurze Darstellung meines in Nordamerika patentierten Dampfbrau- und Kühlapparats; Verlag von Theodor Fischer, Kassel, 1859.
27. Schu, G.; Ruß, W.: Energie; in: Heyse, K.-U. (Hrsg.): Praxishandbuch der Brauerei. Behr’s Verlag, Hamburg, 2000, S. 1–85.
28. Gattermeyer, P.: Mashing Without Primary Energy: „The Way to an Energy-Independent Brewery“; in: MBAA Technical Quarterly 50 (2013), 62–65.
29. Holmes, C.P.; Hense, W.; Donnelly, D. et al.: „Impacts of Steam Injection Technology on Volatile Formation and Stripping During Wort Boiling“; in: MBAA Technical Quarterly 51 (2014), S. 33-41.
30. Pensel, S. (Hrsg.): Handbuch für die praktische Betriebskontrolle [ohne Verlag] [ohne Ort], 1983.
31. Landesgewerbeamt Baden-Württemberg, Zentrale Informationsstelle für Energiefragen (Hrsg.): Rationelle Energienutzung in Brauereien [ohne Verlag u. Ort], 1985.
32. Meyer-Pittroff, R.: Eröffnungsansprache; in: Generaldirektion Telekommunikation, Informationsindustrien und Innovation der Kommission der europäischen Gemeinschaften (Hrsg.): Energiemanagement in der Brauereiwirtschaft. Amt für amtliche Veröffentlichungen der Europäischen Gemeinschaften, Luxemburg, 1990, S. 2–4.
33. Sirchis, J.; Paparella, A.; Tarlowski, K.D.: Das Energiebus-Programm der Gemeinschaften und energietechnische Messungen in Brauereien; in: Generaldirektion Telekommunikation, Informationsindustrien und Innovation der Kommission der europäischen Gemeinschaften (Hrsg.): Energiemanagement in der Brauereiwirtschaft. Amt für amtliche Veröffentlichungen der Europäischen Gemeinschaften, Luxemburg, 1990, S. 43–53.
34. Galitsky, C.; Martin, N.; Worrell, E. et al.: Energy Efficiency Improvement and Cost Saving Opportunities for Breweries, 2003, https://www.energystar.gov/ia/business/industry/LBNL-50934.pdf; Zugriff am: 5.8.2019.
35. Natural Resources Canada: Guide to energy efficiency opportunities in the Canadian Brewing industry, 2011, https://www.nrcan.gc.ca/sites/www.nrcan.gc.ca/files/
oee/files/pdf/publications/industry/Brewers_Guide_access_e.pdf; Zugriff am: 1.9.2019.
36. Carbon Trust: Industrial Energy Efficiency Accelerator – Guide to the brewing sector, 2011, https://www.carbontrust.com/media/206492/ctg058-brewing-industrial-energy-efficiency.pdf; Zugriff am: 5.8.2019.
37. Brewers Association: Energy Usage, GHG Reduction, Efficiency and Load Management Manual [ohne Jahr], https://www.brewersassociation.org/attachments/0001/1530/Sustainability_Energy_Manual.pdf; Zugriff am: 5.8.2019.
38. Campden BRI: 4th worldwide energy efficiency benchmark in the brewing industry [ohne Jahr], https://www.campdenbri.co.uk/services/brewing-energy-benchmark.php; Zugriff am: 8.9.2019.
39. Brewers Association: 2017 SustainabilityBenchmarking Report, 2017, https://s3-us-west-2.amazonaws.com/brewersassoc/wp-content/uploads/2019/01/2017-Sustainability-Benchmarking-Report.pdf; Zugriff am: 1.9.2019.
40. Heyse, K.-U.: „Dr. Georg Schu - Vom Lieblingsgetränk Bier zum Energie- und Umweltspezialisten“; in: Der Weihenstephaner 87 (2019), S. 112–115.
41. Sorrell, S.; Schleich, J.; Scott, S. et al.: Reducing barriers to energy efficiency in private and public organisations. University of Sussex Science Policy Research Unit, Sussex, 2000.
42. Putz, M.; Cherkaskyy, M.; Fanghänel, C. et al.: Energieeffizienzpotzenial in der Planung am Beispiel der Brauerei-Industrie [ohne Jahr], https://www.umwelt.sachsen.de/umwelt/download/4_2_Brauereien.pdf; Zugriff am: 5.8.2019.
43. International Energy Agency: World Energy Outlook 2018; International Energy Agency, Paris, 2018.
44. Andruleit, H.; Franke, D.; Ladage, S. et al.: BGR Energiestudie 2018, 2019, https://www.bgr.bund.de/DE/Themen/Energie/Downloads/energiestudie_2018.pdf__blob=publicationFile&v=10; Zugriff am: 1.9.2019.
45. Remus, C.; Ziolek, A.; Tippkötter, R. et al.: Erarbeitung von Konzepten zur Energieeinsparung sowie zur Optimierung der Energieversorgung in kleinen Unternehmen, 1999, https://www.lanuv.nrw.de/fileadmin/lanuv/veroeffentlichungen/fachberichte/Brauerei99v6.pdf; Zugriff am: 5.8.2019.
46. Pöschko, E.; Grasmück, R.: FB-Vision 2020, 2009, https://www.klimafonds.gv.at/wp-content/uploads/sites/6/BGR42009KB08NE0F40501FSBraucommune.pdf; Zugriff am: 5.8.2019.
47. Schmitt, B.; Lauterbach, C.; Vajen, K.: Branchenkonzept Solare Prozesswärme für Brauereien, 2012, https://www.uni-kassel.de/maschinenbau/fileadmin/datas/fb15/ITE/icons/Bilder_re2/Bilder_OpenSorp/branchenkonzept_solare_prozesswaerme_in_brauereien_-unik-.pdf; Zugriff am: 5.8.2019.
48. Russell, S.T.; Singh, R.P.; Bamforth, C.W.: „Alternative Paradigms for the Production of Beer“; in: Journal of the Institute of Brewing 114 (2008), 349–356.
49. Fischer, W.: Energiewirtschaft der Brauerei. Hans Carl, Nürnberg, 1950.
Name | Datei |
---|---|
Energie als Rohstoff einer Brauerei |
![]() |