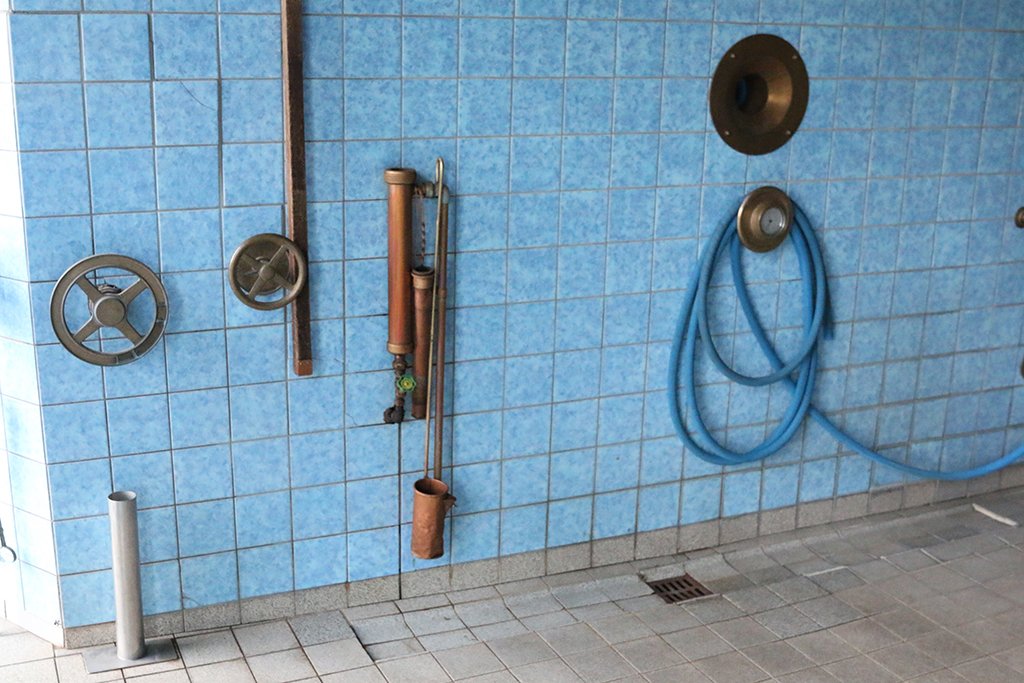
Autor | Institution |
---|---|
Bär, Raik | Lehrstuhl für Brau- und Getränketechnologie, TUM School of Life Science |
Voigt, Tobias | Lehrstuhl für Brau- und Getränketechnologie, TUM School of Life Science |
Datum | 04. Juni 2021 |
Ausgabe | 2 |
Jahrgang | 89 |
Seitenzahl | 69-72 |
Die Produktion von Nahrungsmitteln und Getränken stellt aufgrund von politischen, wirtschaftlichen, ökologischen und sozialen Bedingungen eine Herausforderung für die verarbeitende Industrie dar [1, 2]. Die hohe Marktdynamik, die eine große Produktpalette und eine extrem flexible Produktion erfordern, ist kennzeichnend für die die Getränkeindustrie. Durch eine energieeffiziente Produktion können Kosten nachhaltig gesenkt und die Wettbewerbsfähigkeit gesteigert werden [3, 4]. Die komplexe Getränkeindustrie zeichnet sich durch unterschiedliche Produktionsprozesse mit einer Vielzahl an verschiedenen Maschinen aus. Gerade der Brauprozess ist aufgrund zahlreicher Erhitzungs- und Kühlungsprozesse einer der energieaufwendigsten Herstellungsprozesse in der Lebensmittelindustrie und birgt daher große Einsparpotentiale [1, 5]. In den letzten Jahren gab es verstärkte Bestrebungen, die Energieeffizienz der Getränkeherstellung zu verbessern. Dies wird häufig durch IT-gestützte Maßnahmen und Softwaretools ermöglicht [6]. Gerade für kleine und mittelständische Unternehmen der deutschen Brauindustrie, welche ca. 90 % der Betriebe ausmachen [7], bestehen Barrieren für eine energieeffiziente Produktion. Dabei fehlt es einerseits an Kapital und Kapazität um Energieeinsparmaßnahmen finanzieren und umsetzen zu können. Andererseits spielen fehlendes Know-How im Unternehmen und die fehlende Möglichkeit die laufende Produktion zu unterbrechen eine entscheidende Rolle. Zudem mangelt es an energierelevanten Daten und Informationen aus der Produktion. Meist sind diese unzureichend oder werden nicht ausreichend erfasst [8].
Das Werkzeug der Simulation ermöglicht eine ganzheitliche Betrachtung hinsichtlich des Energie- und Medienbedarfs von Produktionssystemen und kann die Komplexität der Prozesse und Anlagenstrukturen der Getränkeindustrie abbilden.
Das Forschungsprojekt „Hybride Modellierung und Prognose des Medien- und Energiebedarfs in der Getränkeindustrie“ hatte zum Ziel, die Medien- und Energieverbräuche innerhalb der Prozessketten der Getränkeproduktion ganzheitlich, strukturiert und standardisiert darzustellen und zu prognostizieren. Hierzu wurde ein Modellierungseditor „ModEd“ entwickelt, welcher eine einfache, schnelle und strukturierte Modellierung beliebiger Betriebe ohne Vorkenntnisse des Benutzers ermöglicht. Der Editor generiert eine Konfigurationsdatei, welche als Austauschformat für eine automatische Simulationsmodellgenerierung in einer Simulationsumgebung dient [9]. Auf der Basis von umfangreichen Messdaten, aus welchen automatisch benötigte Parameter ermittelt wurden, konnten eine detaillierte Validierung sowie Simulationsstudien durchgeführt werden. Die gesamte Methode ermöglicht es, nicht ausgeschöpfte Potentiale zur Steigerung der Energie- und Medieneffizienz aufzudecken, Optimierungslösungen und innovative Szenarien zur Energieversorgung zu finden und somit mögliche Investitionsentscheidungen bereits im Vorfeld durch fundierte Daten zu begründen.
Systemanalyse
Zu Beginn des Projekts wurden die Systemgrenzen sowie Referenzprozesse festgelegt. Um das reale Verbrauchsverhalten eines Produktionsbetriebes prognostizieren zu können, müssen die Hauptverbraucher der jeweiligen Energie-/Medienart abgebildet werden. Gerade Überlagerungen von Verbräuchen einzelner Units können zu enormen Lastspitzen führen. Das Verbrauchsverhalten von Anlagen im Batch-Bereich ist abhängig vom aktuell ablaufenden Prozess, wohingegen das Verbrauchsverhalten bei Maschinen im Verpackungsbereich abhängig vom aktuell anliegenden Betriebszustand ist [10]. Um eine geeignete Modellierungs- und Simulationstiefe festzulegen wurde auf bereits bestehende Standardisierungen zurückgegriffen. Die ISA-88-Norm beschreibt die Einteilung von batch-orientierten Produktionsbetrieben und unterscheidet zwischen physischen Modell, Prozess-, Rezept- sowie dem Produktionsplanmodell [11]. Abbildung 1 zeigt ein Beispiel für eine Zuordnung des Sudhauses als Process Cell und dem Maischbottich als untergeordnete Unit mit einem entsprechenden Prozess. Im Fall einer Getränkeabfüllanlage entspricht das Unit-Level bspw. einer Füllmaschine. Als geeignete Granularität wurde die „Unit-Ebene“ im physischen Modell, sowie die „Process Operation-Ebene“ im Prozessmodell festgelegt. Eine tiefere Ebene würde zwar detailliertere Ergebnisse der Simulation liefern, gleichzeitig aber eine höhere Anzahl an benötigten Parametern bedeuten.
Modellierung
Der entwickelte Modellierungseditor „ModEd“ hat zum Ziel, schnell und ohne spezifisches Vorwissen des Benutzers, ein Modell eines Produktionssystems zu erstellen. Hierfür wurde eine benutzerfreundliche Software zur grafischen Modellierung folgender vier Modellierungssäulen entwickelt.
Das Anlagenmodell wird in einzelnen Process Cells (z.B. Sudhaus, Getränkeabfüllanlage) durch vordefinierte, in einer Bibliothek hinterlegte, Bausteine modelliert. Diese unterscheiden sich grundlegend durch das Energieverbrauchsverhalten sowie durch den Parametersatz (Technische Daten, Ausfall- und Verbrauchsverhalten). Die Bibliothek bildet die in der Getränkeindustrie am häufigsten vorkommenden Aggregate, aufgeteilt in die Bereiche Batch, Verpackung und Sonstige ab. Abbildung 2 zeigt die Oberfläche zur Modellierung einer Process Cell (Getränkeabfüllanlage) im physischen Modell des Modellierungseditors. Abbildung 3 (oben) zeigt das Modell eines Sudhauses.
Das Prozessmodell beschreibt die ablaufenden Prozesse im Batch-Bereich und ist nach [11] untergliedert. Die Modellierung basiert auf der Modellierungssprache BPMN (Business Process Model and Notation Language). Modelliert wird beginnend auf der „Process“-Ebene, über die „Process-Stage“-Ebene bis zur „Process-Operation“-Ebene (vgl. Abbildung 3 unten). Die „Process-Operation“-Ebene stellt die verbrauchsrelevante Ebene, in welcher die „Process Operations“ frei definierbar sind, dar. Neben der Dauer werden die entsprechenden Mengen an Energie und Medien (thermische Energie, elektrische Energie, Wasser, Druckluft, CO2), welche für die entsprechende „Process Operation“ benötigt werden, parametrisiert.
Das Rezept-/Artikelmodell beschreibt Produkte, welche in Process Cells produziert werden können. Im Batch-Bereich werden alle Rezepte (z.B. Helles, Weißbier) angelegt und ein im Vorfeld erstelltes Prozessmodell mit einem physischen Modell verknüpft. Die Verknüpfung erfolgt über Process Stages und Units und bietet somit eine sehr hohe Variabilität in der Modellierung. Im Verpackungsbereich werden alle Artikel, welche auf Verpackungsanlagen produziert werden können, angelegt und parametrisiert. Die Artikel beschreiben bspw. das abzufüllende Produkt, den Flaschentyp sowie deren Ausstattung. Alle Maschinen können mit artikelspezifischen Parametern versehen werden.
Das Produktionsablaufmodell verknüpft das Rezept-/Artikelmodell sowie das physische Modell, um eine anlagenspezifische Abfolge von Rezepten und Artikeln abzubilden. Hierfür wurde ein Konzept mit mehreren Zeitmodellen entwickelt, welche die Produktionszeiträume sowie die Zeiten zwischen einzelnen Aufträgen definiert. Das Schichtenmodell definiert eine Beschränkung in welchem Zeitraum auf einer Anlage eine Produktion stattfinden darf. In einem Matrizenmodell werden im Batch-Bereich Zeiten für die Sudfolge zwischen einzelnen Suden für jede mögliche Rezeptkombination anlagenspezifisch hinterlegt. Im Verpackungsbereich werden die Umstell- und Reinigungszeiten zwischen den einzelnen Artikeln spezifisch je Verpackungsanlage definiert. Das Ablaufmodell legt die Auftragsabfolge je Process Cell fest.
Durch die Funktionalität des Modellierungseditors werden die einzelnen Säulen miteinander verknüpft und die simulationsrelevanten Daten in einer XML-Konfigurationsdatei festgehalten. Diese stellt die Grundlage für das automatische Generieren eines Simulationsmodells in einer beliebigen Simulationsumgebung dar.
Parameterermittlung
Eine wesentliche Herausforderung bei der Modellierung ist die Verfügbarkeit der simulationsrelevanten Parameter. Daher wurde das Softwaretool „ddAnalyzer“, zur automatischen Berechnung von Simulationsparametern sowie zur Auswertung von Simulationsläufen, in MATLAB 2020b (App Designer) entwickelt. Das Tool basiert auf einer Datenbankstruktur, in welche einerseits die real erhobenen Daten transferiert wurden und in welcher andererseits die Simulationsergebnisse ausgegeben werden.
Simulation
Ziel war es, in Zusammenarbeit mit der SimPlan AG, eine Simulationsumgebung zur gleichzeitigen Simulation von Batch- und damit kontinuierlichen Prozessen und dem diskreten Betrieb von Verpackungsmaschinen hinsichtlich deren Energie- und Medienverbrauch zu entwickeln. Verwendet wurde das bereits bestehende Simulationstool „PacSi“, welches die Simulation von Verpackungsprozessen beherrscht. Die Software verfolgt einen zeitdiskreten Ansatz hinsichtlich der angewendeten Methode und basiert auf der Simulation des Materialflusses. Im Laufe des Projekts wurden zahlreiche Funktionalitäten zur Erweiterung des Simulationssystems erarbeitet und implementiert. Eine grundlegende Neuentwicklung stellt die automatische Simulationsmodellgenerierung auf Basis der XML-Austauschdatei dar. Zur Abbildung des Batch-Bereichs wurde ein neuartiger Batch-Baustein, welcher abweichend zu den Bausteinen des diskreten Bereichs, auf einer zeitabhängigen Vorgabe der einzelnen Prozessoperationen basiert. Eine Besonderheit stellt die Einbindung eines Produktionsplans, d. h. der Ablauf von verschiedenen Rezepten und Artikeln dar. Dies ermöglicht unter anderem die Simulation komplexer Produktionssysteme über einen längeren Zeitraum.
Zur Validierung der Methode wurden ein Sudhaus und eine Getränkeabfüllanlage im Modellierungseditor abgebildet und Produktionspläne, welche in real stattgefunden haben, inkl. aller Prozesse, Rezepte und Artikel modelliert. Die Zeiträume umfassen mitunter eine Dauer von ca. einer Woche und sind unter anderem durch Unterbrechungen, wie z.B. durch ein Wochenende gekennzeichnet. Nach der automatischen Generierung des jeweiligen Simulationsmodells konnten die Zeiträume simuliert und die ermittelten Verbrauchswerte mit den real gemessenen Werten unit-spezifisch verglichen werden. Im Batch-Bereich konnte eine Gesamtabweichung des thermischen Energiebedarfs von 2,2 % und des elektrischen Energiebedarfs von 4,2 % erreicht werden (Zeitraum 7 Tage; 71 Sude, 3 Rezepte). Für die Getränkeabfüllanlage wurde eine Abweichung des elektrischen Energiebedarfs von 0,52 % (Zeitraum 8 Tage, 4 Artikel) sowie eine Abweichung des Druckluftbedarfs von 0,14 % (Zeitraum 2,6 Tage, 2 Artikel) erreicht. Zusätzlich konnten geringe Abweichungen für den Bedarf an Wasser, CO2 sowie thermischer Energie erzielt werden. Abbildung 4 zeigt einen Ausschnitt des Verlaufs des gemessenen und simulierten elektrischen Leistungsbedarfs der Getränkeabfüllanlage in einem Validierungszeitraum.
Simulationsexperiment
Auf Grundlage der Modelle der Validierung konnten Simulationsexperimente durchgeführt werden. Ziel einer Simulationsstudie war es, anhand des Modells des Sudhauses, mit einem realen Produktionsplan eine Reduzierung der Spitzenlasten des thermischen Energiebedarfs durch eine Anpassung der Zeiten zwischen den einzelnen Suden zu erreichen. Die Simulationsdauer umfasst einen Zeitraum von 7 Tagen, in welchem insgesamt 71 Batches aus drei verschiedenen Rezepturen hergestellt werden. Abbildung 5 zeigt einen Ausschnitt aus dem Vergleich der thermischen Energiebedarfskurven des Sudhauses vor und nach der Anpassung der Sudfolge. Dabei konnte eine theoretische Reduzierung der Spitzenlasten von bis zu 32 % (vgl. Detail der Abbildung) erreicht werden.
Fazit
Die im Forschungsprojekt „HyMo_ME“ entwickelte Methode bietet eine Möglichkeit hybride Produktionssysteme ganzheitlich hinsichtlich ihres Energie- und Medienbedarfs zu modellieren und simulieren. Eine durchgängige und simple Anwendung des ModEds sowie der Parameterermittlungs- und Auswertetools bieten gerade für KMU eine Chance ohne spezifisches Vorwissen Optimierungspotentiale aufzudecken und die Energie- und Medieneffizienz zu erhöhen. Dies konnte durch eine umfangreiche Validierung sowie anhand von Simulationsexperimenten gezeigt werden.
Weitere Informationen finden Sie auf www.hymome.wzw.tum.de.
Danksagung
Das Forschungsprojekt wurde durch die Bayerische Forschungsstiftung (AZ-1217-16) gefördert. Vielen Dank an Sebastian Schmid und Dr. Karl Glas, Lehrstuhl für Lebensmittelchemie und Molekulare Sensorik, Technische Universität München für die Erfassung und Bereitstellung von Messdaten im gemeinsamen Projekt HyMo_ME.
Name | Datei |
---|---|
Simulation von Energie- und Medienverbräuche in der Brauerei |
![]() |